Informe de resolución de problemas 8D
8D es un método de resolución de problemas utilizado globalmente, principalmente en la industria manufacturera, por ingenieros de calidad y gerentes de operaciones. El propósito del método de resolución de problemas 8D es identificar, corregir y prevenir problemas que afectan a los clientes y la eficiencia operativa. Es un enfoque de resolución de problemas similar al ciclo PDCA (Planificar – Hacer – Verificar – Actuar).
8D significa 8 Disciplinas. Es una metodología que enfatiza «Ningún problema debe repetirse, sino solucionarse permanentemente».
El método de resolución de problemas 8D evolucionó originalmente durante la Segunda Guerra Mundial. Pero se convirtió en una metodología oficial en 1974, cuando fue utilizado por EE. UU. Gobierno para sus Operaciones Militares como ‘Military Standard 1520’. Posteriormente fue adaptado y popularizado por Ford Motors con una ligera modificación en la metodología.
Como su nombre indica 8D tiene 8 disciplinas que cualquier proceso u operación debe seguir para resolver los problemas que ocurren. El resultado de 8D es un informe llamado ‘Informe 8D’ que registra los problemas, las causas raíz y las acciones correctivas y preventivas.
A continuación son las D en el enfoque 8D:
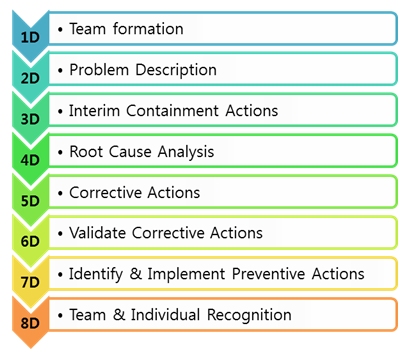
Figura 1: Enfoque de resolución de problemas 8D
1D – Formación de equipos:
El primer y más importante paso no solo en 8D sino también en cualquier otra iniciativa o proyecto es la Formación de equipos, ya que ninguna iniciativa puede tener éxito sin un equipo adecuado. El equipo seleccionado debe ser comprometido, competente, coordinado, multifuncional con representación de todos los equipos y debe tener conocimiento de la metodología 8D.
2D – Descripción del problema:
Después de seleccionar el equipo, nuestra concentración debe estar en detallar el problema. El equipo debe recopilar detalles sobre el problema para comprender completamente la profundidad del problema. Todos los detalles deben estar basados en datos y hechos.
3D – Acciones de contención provisionales:
Una vez que se describe el problema, antes de comenzar a resolverlo, el equipo debe corregir el efecto del problema, especialmente en clientes. Puede implicar acciones como aislar los artículos afectados, reemplazar las piezas defectuosas, antes de que llegue a los clientes. Este paso es principalmente para evitar que el problema llegue al mercado y a los clientes, lo que podría convertirse en una desventaja competitiva y reducir la lealtad del cliente.
4D – Análisis de causa raíz:
Después de tomar acciones de contención, el equipo debe Involucrar en identificar la (s) causa (s) raíz del problema. Se pueden utilizar métodos y herramientas como el análisis de los 5 motivos, el diagrama de espina de pescado, el análisis de Pareto, las 7 herramientas de CC antiguas, las herramientas de CC nuevas, etc., para identificar la causa raíz. Un punto importante a tener en cuenta es: Cualquiera que sea el método que se utilice para RCA, debe basarse en datos & hechos.
5D – Formular acciones correctivas:
Después de llegar con éxito a la causa raíz, el equipo debe formular las acciones correctivas que se tomarán para corregir el problema. Se pueden utilizar herramientas como lluvia de ideas, diagrama de afinidad, etc.
6D – Validar acciones correctivas:
Después de llegar a las acciones correctivas, el equipo debe validar si las soluciones son efectivas. Hay varias herramientas como pruebas de vida acelerada, simulación, etc. disponibles para este propósito. Entonces la solución se puede implementar en el proceso. El enfoque de solución del paso 4-6 debe repetirse hasta que el problema se elimine por completo.
7D – Acción preventiva:
La identificación e implementación de acciones correctivas es solo una solución temporal que mantiene el sistema en funcionamiento o está como ‘Vivir con el problema tomando contramedidas’. La solución permanente es identificar una posible solución a largo plazo que no permita que el problema (problemas similares) vuelva a ocurrir en el sistema. A veces, la acción correctiva será una medida costosa y con tiempo. La acción preventiva realiza cambios en el sistema, procesos ascendentes o descendentes para que todo el sistema se modifique o alinee para operaciones ‘sin problemas’.
8D – Reconocimiento individual y en equipo:
Una vez que el problema está completamente resuelto, el equipo y los contribuyentes extraordinarios deben ser recompensados y reconocidos adecuadamente. Esto actuará como un factor de motivación para otros empleados.
Estos son los pasos de la metodología 8D. En resumen, 8D es una metodología holística, sistemática y probada para la resolución de problemas.