8D問題解決レポート
8Dは、主に製造業で品質エンジニアと運用管理者によってグローバルに使用されている問題解決方法です。 8D問題解決方法の目的は、顧客と運用効率に影響を与える問題を特定、修正、防止することです。これは、PDCAサイクル(計画-実行-チェック-行動)に似た問題解決アプローチです。
8Dは8分野の略です。 「問題は繰り返さないが恒久的に修正する」ことを強調する方法論です。
8D問題解決方法は、もともと第二次世界大戦中に発展しましたが、1974年に米国で使用されたときに公式の方法論になりました。 「軍用規格1520」としての軍事作戦のための政府。その後、方法論をわずかに変更して、フォードモーターズによって採用され、普及しました。
名前が示すように、8Dには8つの分野があります。 8Dの結果は、問題、根本原因、修正および予防措置を記録した「8Dレポート」と呼ばれるレポートです。
以下を参照してください。 8DアプローチのDは次のとおりです。
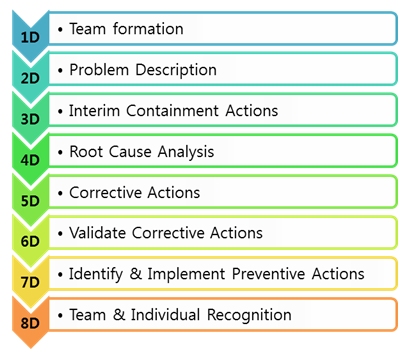
図1:8D問題解決アプローチ
1D –チーム編成:
8Dだけでなく、他のイニシアチブまたはプロジェクトでも最初の最も重要なステップはチーム編成です。どのイニシアチブも成功することはできません。適切なチームなしで。選択するチームは、献身的で、有能で、調整され、すべてのチームの代表と連携し、8D方法論に精通している必要があります。
2D –問題の説明:
チームを選択した後、問題の詳細に集中する必要があります。チームは、問題の深さを完全に理解するために、問題に関する詳細を収集する必要があります。すべての詳細はデータと事実に基づいている必要があります。
3D–暫定的な封じ込めアクション:
問題が説明されたら、問題解決に進む前に、チームは問題の影響を修正する必要があります。顧客。顧客に届く前に、影響を受けるアイテムを分離したり、欠陥のある部品を交換したりするなどのアクションが含まれる場合があります。このステップは主に、問題が市場や顧客に到達するのを防ぎ、競争上の不利益となり、顧客の忠誠心を低下させる可能性があることを防ぐためです。
4D –根本原因分析:
封じ込め措置を講じた後、チームは問題の根本原因の特定に関与します。 5-なぜ分析、フィッシュボーン図、パレート分析、7つの古いQCツール、新しいQCツールなどの方法とツールを使用して、根本原因を特定できます。注意すべき重要な点は、RCAに使用する方法が何であれ、データ&ファクトベースである必要があるということです。
5D –是正措置の策定:
根本原因に到達した後、チームは問題を是正するために取るべき是正措置を策定する必要があります。ブレーンストーミング、アフィニティ図などのツールを使用できます。
6D –修正措置の検証:
是正措置に到達した後、チームはソリューションが効果的であるかどうかを検証する必要があります。この目的のために利用可能な加速寿命試験、シミュレーションなどのようないくつかのツールがあります。次に、ソリューションをプロセスに実装できます。手順4〜6の解決策のアプローチは、問題が完全に解消されるまで繰り返す必要があります。
7D –予防措置:
是正措置の特定と実装は、システムの稼働を維持するための一時的な解決策にすぎません。 「対策を講じて問題を抱えて生きる」のように。恒久的な解決策は、問題(同様の問題)がシステムに再び発生することを許可しない潜在的な長期的な解決策を特定することです。場合によっては、是正措置は費用がかかり、当面の措置となります。予防措置により、システム、アップストリームまたはダウンストリームプロセスが変更され、システム全体が「問題のない」操作のために変更または調整されます。
8D –チームおよび個人の認識:
問題が完全に解消されたら解決するには、チームと並外れた貢献者に報酬を与え、適切に認識させる必要があります。これは、他の従業員のモチベーション要因として機能します。
これらは8D方法論のステップです。要約すると、8Dは、問題解決のための全体的で体系的で実証済みの方法論です。