8D 문제 해결 보고서
8D는 주로 품질 엔지니어 및 운영 관리자가 제조 산업에서 전 세계적으로 사용하는 문제 해결 방법입니다. 8D 문제 해결 방법의 목적은 고객 및 운영 효율성에 영향을 미치는 문제를 식별, 수정 및 예방하는 것입니다. PDCA주기 (Plan – Do – Check – Act)와 유사한 문제 해결 접근 방식입니다.
8D는 8 개 분야를 나타냅니다. “문제는 반복되지 않고 영구적으로 고쳐 져야한다”를 강조하는 방법론입니다.
8D 문제 해결 방법은 원래 2 차 세계 대전 때 진화했지만 1974 년 미국에서 사용되면서 공식적인 방법론이되었습니다. 군사 작전을위한 정부는 ‘Military Standard 1520’으로 지정되었습니다. 나중에 Ford Motors에서 방법론을 약간 수정하여 채택하고 대중화했습니다.
이름에서 알 수 있듯이 8D에는 8 개 분야가 있습니다. 8D의 결과는 문제, 근본 원인, 시정 및 예방 조치를 기록하는 ‘8D 보고서’라는 보고서입니다.
아래는 8D 접근 방식의 D는 다음과 같습니다.
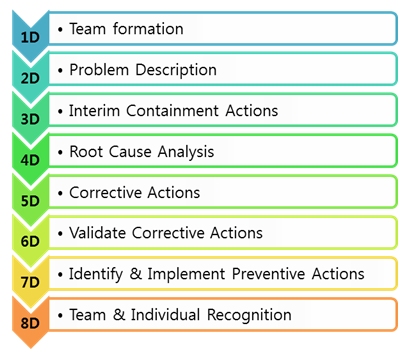
그림 1 : 8D 문제 해결 접근 방식
1D – 팀 구성 :
8D뿐만 아니라 다른 이니셔티브 또는 프로젝트에서도 첫 번째이자 가장 중요한 단계는 팀 구성입니다. 어떤 이니셔티브도 성공할 수 없기 때문입니다. 적절한 팀없이. 선택된 팀은 헌신적이고, 유능하며, 조정되고, 모든 팀의 대표와 상호 작용해야하며, 8D 방법론에 대한 지식이 있어야합니다.
2D – 문제 설명 :
팀을 선택한 후에는 문제를 자세히 설명하는 데 집중해야합니다. 팀은 문제의 깊이를 완전히 이해하기 위해 문제에 대한 세부 정보를 수집해야합니다. 모든 세부 사항은 데이터와 사실을 기반으로해야합니다.
3D – 임시 격리 조치 :
문제가 설명되면 문제 해결을 시작하기 전에 팀은 특히 문제의 영향을 수정해야합니다. 고객. 고객에게 전달되기 전에 영향을받는 품목을 분리하고 결함이있는 부품을 교체하는 등의 조치가 포함될 수 있습니다. 이 단계는 주로 문제가 시장과 고객에게 전달되는 것을 방지하기위한 것입니다. 이는 경쟁에서 불리하게 될 수 있고 고객 충성도를 떨어 뜨릴 수 있습니다.
4D – 근본 원인 분석 :
격리 조치를 취한 후 팀은 문제의 근본 원인을 식별하는 데 관여합니다. 5-Why Analysis, Fishbone 다이어그램, Pareto Analysis, 7 개의 Old QC 도구, New QC 도구 등과 같은 방법 및 도구를 사용하여 근본 원인을 식별 할 수 있습니다. 주목해야 할 중요한 점은 RCA에 사용되는 방법이 무엇이든간에 데이터 & 사실 기반이어야합니다.
5D – 시정 조치 공식화 :
근본 원인에 성공적으로 도달 한 후 팀은 문제를 해결하기 위해 취해야 할 시정 조치를 공식화해야합니다. 브레인 스토밍, 선호도 다이어그램 등의 도구를 사용할 수 있습니다.
6D – 시정 조치 확인 :
시정 조치에 도달 한 후 팀은 솔루션이 효과적인지 확인해야합니다. 이를 위해 사용 가능한 가속 수명 테스트, 시뮬레이션 등과 같은 여러 도구가 있습니다. 그런 다음 프로세스에서 솔루션을 구현할 수 있습니다. 문제가 완전히 제거 될 때까지 4-6 단계의 솔루션 접근 방식을 반복해야합니다.
7D – 예방 조치 :
시정 조치를 식별하고 구현하는 것은 시스템을 계속 실행하는 임시 솔루션 일뿐입니다. ‘대책을 통해 문제와 함께 살아 가기’처럼요. 영구적 인 해결책은 문제 (유사한 문제)가 시스템에 다시 발생하는 것을 허용하지 않는 잠재적 인 장기적인 해결책을 식별하는 것입니다. 때로는 시정 조치가 비용이 많이 들고 측정하는 데 시간이 걸립니다. 예방 조치는 시스템, 업스트림 또는 다운 스트림 프로세스를 변경하여 전체 시스템이 ‘문제없는’작업을 위해 수정되거나 조정되도록합니다.
8D – 팀 및 개인 인식 :
문제가 완전히 해결되면 해결되면 팀과 특별한 공헌자는 보상을 받고 적절하게 인정 받아야합니다. 이것은 다른 직원들에게 동기 부여 요소로 작용할 것입니다.
8D 방법론의 단계입니다. 요약하면 8D는 문제 해결을위한 전체적이고 체계적이며 입증 된 방법론입니다.