8D-problemløsingsrapport
8D er en problemløsningsmetode som brukes globalt, hovedsakelig i produksjonsindustrien av Quality Engineers og Operations managers. Formålet med 8D problemløsningsmetode er å identifisere, rette og forhindre problemer som påvirker kunder og driftseffektivitet. Det er en problemløsningsmetode som ligner på PDCA-syklusen (Plan – Do – Check – Act).
8D står for 8 disipliner. Det er en metodikk som understreker «Ingen problemer skal gjentas men løses permanent».
8D Problem Solving Method opprinnelig utviklet seg under andre verdenskrig. Men det ble en offisiell metode i 1974, da den ble brukt av USA Regjeringen for sine militære operasjoner som «Military Standard 1520». Senere ble den tilpasset og popularisert av Ford Motors med liten modifikasjon i metodikken.
Som navnet antyder, har 8D 8 disipliner at enhver prosess eller operasjoner skal følge for å løse problemene som oppstår. Resultatet av 8D er en rapport kalt ‘8D Report’ som registrerer problemene, grunnårsaken (e) og korrigerende og forebyggende handlinger.
Nedenfor er D-ene i 8D-tilnærming:
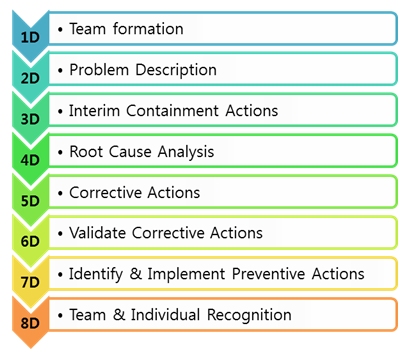
Figur 1: 8D Problemløsningsmetode
1D – Team Formation:
Det første og viktigste trinnet ikke bare i 8D, men også i ethvert annet initiativ eller prosjekt, er Team Formation, for ethvert initiativ kan ikke lykkes uten riktig lag. Teamet som er valgt skal være engasjert, kompetent, koordinert, tverrfunksjonelt med representasjon fra alle lag, og skal være kunnskapsrik i 8D-metodikk.
2D – Problembeskrivelse:
Når vi har valgt teamet, bør vi konsentrere oss om å detaljere problemet. Teamet bør samle inn detaljer om problemet for å forstå problemets dybde. Alle detaljer skal være data- og faktabaserte.
3D – Midlertidige inneslutningshandlinger:
Når problemet er beskrevet, før teamet går opp til problemløsing, bør teamet løse effekten av problemet, spesielt på kunder. Det kan innebære handlinger som å isolere elementene som er berørt, erstatte defekte deler før det når kundene. Dette trinnet er hovedsakelig for å forhindre at problemet når markedet og kundene, noe som kan bli en konkurransemessig ulempe og redusere kundelojaliteten.
4D – Rotårsaksanalyse:
Etter å ha tatt inneslutningshandlinger, bør teamet involverer i å identifisere årsaken (e) til problemet. Metoder og verktøy som 5-Why Analysis, Fishbone diagram, Pareto Analysis, 7 Old QC tools, New QC tools etc. kan brukes til å identifisere grunnårsaken. Et viktig poeng å merke seg er: Uansett hvilken metode som brukes for RCA, bør det være data & faktabasert.
5D – Formuler korrigerende tiltak:
Etter å ha kommet til grunnårsaken, bør teamet formulere korrigerende tiltak for å rette opp problemet. Verktøy som Brain storming, Affinity diagram etc. kan brukes.
6D – Valider korrigerende tiltak: tter å ha kommet til de korrigerende tiltakene, bør teamet validere om løsningene er effektive. Det er flere verktøy som Accelerated life testing, simulation etc. tilgjengelig for dette formålet. Da kan løsningen implementeres i prosessen. Løsningsmetoden fra trinn 4-6 bør gjentas til problemet er fullstendig eliminert.
7D – Forebyggende handling:
Å identifisere og implementere korrigerende handlinger er bare en midlertidig løsning som holder systemet i gang eller er som ‘Å leve med problemet ved å ta mottiltak’. Den permanente løsningen er å identifisere en potensiell langsiktig løsning som ikke vil tillate at problemet (lignende problemer) oppstår i systemet igjen. Noen ganger vil korrigerende tiltak være et kostbart tiltak. Forebyggende handling gjør endringer i systemet, oppstrøms eller nedstrøms prosesser slik at hele systemet blir modifisert eller justert for «Problemfri» operasjoner.
8D – Team og individuell anerkjennelse:
Når problemet er fullstendig løst, må teamet og de ekstraordinære bidragsyterne belønnes og anerkjennes på riktig måte. Dette vil fungere som en motivasjonsfaktor for andre ansatte.
Dette er trinnene i 8D-metodikken. For å oppsummere er 8D en helhetlig, systematisk og velprøvd metodikk for problemløsning.