8D Probleemoplossingsrapport
8D is een methode voor het oplossen van problemen die wereldwijd wordt gebruikt, voornamelijk in de maakindustrie door Quality Engineers en Operations-managers. Het doel van de 8D-methode voor het oplossen van problemen is het identificeren, corrigeren en voorkomen van problemen die klanten en operationele efficiëntie beïnvloeden. Het is een probleemoplossende benadering vergelijkbaar met de PDCA-cyclus (Plan – Do – Check – Act).
8D staat voor 8 Disciplines. Het is een methodologie die de nadruk legt op “Geen probleem moet worden herhaald, maar permanent worden opgelost”.
8D Probleemoplossingsmethode is oorspronkelijk ontwikkeld tijdens de Tweede Wereldoorlog. Maar het werd een officiële methodologie in 1974, toen het werd gebruikt door de VS Regering voor haar militaire operaties als ‘Military Standard 1520’. Later werd het aangepast en gepopulariseerd door Ford Motors met een kleine wijziging in de methodologie.
Zoals de naam aangeeft heeft 8D 8 disciplines dat elk proces of elke handeling moet volgen om de optredende problemen op te lossen. Het resultaat van 8D is een rapport genaamd ‘8D Report’ dat de problemen, hoofdoorzaak (en) en corrigerende en preventieve maatregelen registreert.
Het onderstaande zijn de D’s in 8D-benadering:
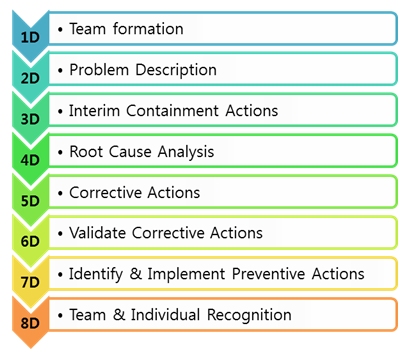
Figuur 1: 8D-aanpak voor probleemoplossing
1D – Teamvorming:
De eerste en belangrijkste stap, niet alleen in 8D maar ook in elk ander initiatief of project, is teamvorming, want elk initiatief kan niet succesvol zijn zonder een goed team. Het geselecteerde team moet betrokken, bekwaam, gecoördineerd, multifunctioneel zijn met vertegenwoordiging van alle teams, en moet kennis hebben van 8D-methodologie.
2D – Probleembeschrijving:
Nadat we het team hebben geselecteerd, zouden we ons moeten concentreren op het beschrijven van het probleem. Het team moet details over het probleem verzamelen om de diepte van het probleem volledig te begrijpen. Alle details moeten gebaseerd zijn op gegevens en feiten.
3D – Tussentijdse inperkingsacties:
Zodra het probleem is beschreven, moet het team het effect van het probleem oplossen, vooral op klanten. Het kan gaan om acties zoals het isoleren van de getroffen items, het vervangen van defecte onderdelen voordat deze de klanten bereiken. Deze stap is voornamelijk bedoeld om te voorkomen dat het probleem de markt en klanten bereikt, wat een concurrentienadeel kan worden en de loyaliteit van de klant kan verminderen.
4D – Analyse van de hoofdoorzaak:
Na het nemen van inperkingsmaatregelen moet het team betrokken zijn bij het identificeren van de hoofdoorzaak (en) van het probleem. Methoden en tools zoals 5-Why-analyse, Fishbone-diagram, Pareto-analyse, 7 oude QC-tools, nieuwe QC-tools enz. Kunnen worden gebruikt om de hoofdoorzaak te identificeren. Een belangrijk punt om op te merken is: welke methode er ook wordt gebruikt voor RCA, het moet op gegevens & gebaseerd zijn op feiten.
5D – Formuleer corrigerende maatregelen:
Nadat met succes de hoofdoorzaak is gevonden, moet het team corrigerende maatregelen formuleren om het probleem te verhelpen. Tools zoals Brain Storming, Affiniteitsdiagram etc. kunnen worden gebruikt.
6D – Valideer corrigerende maatregelen:
Nadat het team tot de corrigerende maatregelen is gekomen, moet het valideren of de oplossingen effectief zijn. Hiervoor zijn verschillende tools zoals Accelerated life testing, simulatie etc. beschikbaar. Vervolgens kan de oplossing in het proces worden geïmplementeerd. De oplossingsbenadering van stap 4-6 moet worden herhaald totdat het probleem volledig is verholpen.
7D – Preventieve maatregelen:
Het identificeren en implementeren van corrigerende maatregelen is slechts een tijdelijke oplossing die ervoor zorgt dat het systeem blijft draaien of zoals ‘Leven met het probleem door tegenmaatregelen te nemen’. De permanente oplossing is het identificeren van een mogelijke langetermijnoplossing waardoor het probleem (soortgelijke problemen) niet opnieuw in het systeem kan optreden. Soms zijn corrigerende maatregelen een kostbare, tijdrovende maatregel. Preventieve actie brengt wijzigingen aan in het systeem, stroomopwaartse of stroomafwaartse processen, zodat het hele systeem wordt aangepast of uitgelijnd voor ‘probleemloze’ bewerkingen.
8D – Team- en individuele herkenning:
Zodra het probleem volledig is opgelost, moeten het team en de buitengewone bijdragers op passende wijze worden beloond en erkend. Dit werkt als een motivatiefactor voor andere werknemers.
Dit zijn de stappen van de 8D-methodologie. Samenvattend is 8D een holistische, systematische en bewezen methodologie voor het oplossen van problemen.