Raport rozwiązywania problemów 8D
8D to metoda rozwiązywania problemów stosowana na całym świecie, głównie w przemyśle wytwórczym przez inżynierów jakości i menedżerów operacyjnych. Celem metody rozwiązywania problemów 8D jest identyfikacja, korygowanie i zapobieganie problemom wpływającym na klientów i efektywność operacyjną. Jest to podejście do rozwiązywania problemów podobne do cyklu PDCA (Plan – Do – Check – Act).
8D oznacza 8 dyscyplin. Jest to metodologia, która kładzie nacisk na „Żaden problem nie powinien być powtarzany, ale naprawiany na stałe”.
Metoda rozwiązywania problemów 8D pierwotnie rozwinęła się podczas drugiej wojny światowej. Jednak stała się oficjalną metodologią w 1974 roku, kiedy została zastosowana przez USA Rząd za swoje operacje wojskowe jako „Standard wojskowy 1520”. Później został zaadaptowany i spopularyzowany przez Ford Motors z niewielkimi zmianami w metodyce.
Jak sama nazwa wskazuje, 8D ma 8 dyscyplin że jakikolwiek proces lub operacje powinny być wykonane w celu rozwiązania występujących problemów. Wynikiem 8D jest raport o nazwie „Raport 8D”, który rejestruje problemy, przyczyny źródłowe oraz działania naprawcze i zapobiegawcze.
Poniżej to D w podejściu 8D:
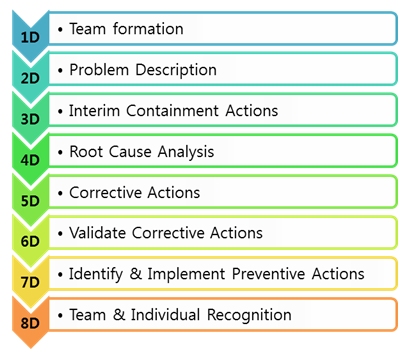
Rysunek 1: Podejście do rozwiązywania problemów 8D
1D – Tworzenie zespołu:
Pierwszym i najważniejszym krokiem nie tylko w 8D, ale także w każdej innej inicjatywie lub projekcie jest formowanie zespołu, ponieważ żadna inicjatywa nie może się udać bez odpowiedniego zespołu. Wybrany zespół powinien być zaangażowany, kompetentny, skoordynowany, wszechstronny z reprezentacją wszystkich zespołów i powinien posiadać wiedzę w zakresie metodologii 8D.
2D – Opis problemu:
Po wybraniu zespołu powinniśmy skupić się na szczegółowym opisaniu problemu. Zespół powinien zebrać szczegółowe informacje o problemie, aby w pełni zrozumieć głębię problemu. Wszystkie szczegóły powinny opierać się na danych i faktach.
3D – Tymczasowe działania powstrzymujące:
Po opisaniu problemu, przed przystąpieniem do rozwiązywania problemu, zespół powinien naprawić jego wpływ, zwłaszcza na klienci. Może obejmować działania, takie jak izolowanie elementów, których dotyczy problem, wymiana wadliwych części, zanim dotrą one do klientów. Ten krok ma głównie na celu zapobieżenie dotarciu problemu na rynek i klientów, co może stać się niekorzystne dla konkurencji i zmniejszyć lojalność klientów.
4D – Analiza przyczyn źródłowych:
Po podjęciu działań powstrzymujących zespół powinien zaangażować w identyfikację pierwotnej przyczyny (przyczyn) problemu. Metody i narzędzia, takie jak analiza 5-Why, diagram Fishbone, analiza Pareto, 7 starych narzędzi do kontroli jakości, nowe narzędzia do kontroli jakości itp., Mogą być użyte do zidentyfikowania pierwotnej przyczyny. Ważną kwestią, na którą należy zwrócić uwagę, jest: jakakolwiek metoda jest używana do RCA, powinna opierać się na danych & faktach.
5D – Sformułuj działania naprawcze:
Po pomyślnym znalezieniu przyczyny źródłowej zespół powinien sformułować działania naprawcze, które należy podjąć w celu naprawienia problemu. Można użyć narzędzi takich jak burza mózgów, diagram powinowactwa itp.
6D – Sprawdź poprawność działań:
Po podjęciu działań naprawczych zespół powinien zweryfikować, czy rozwiązania są skuteczne. W tym celu dostępnych jest kilka narzędzi, takich jak przyspieszone testowanie żywotności, symulacja itp. Następnie rozwiązanie może zostać wdrożone w procesie. Podejście do rozwiązania z kroku 4-6 powinno być powtarzane, aż problem zostanie całkowicie wyeliminowany.
7D – Działanie zapobiegawcze:
Identyfikacja i wdrożenie działań naprawczych to tylko tymczasowe rozwiązanie, które utrzymuje działanie systemu lub jest jak „Życie z problemem poprzez podejmowanie środków zaradczych”. Trwałym rozwiązaniem jest zidentyfikowanie potencjalnego długoterminowego rozwiązania, które nie pozwoli na ponowne pojawienie się problemu (podobnych problemów) w systemie. Czasami działania naprawcze będą kosztowne i czasochłonne. Działanie zapobiegawcze wprowadza zmiany w systemie, w procesach poprzedzających lub końcowych, tak że cały system jest modyfikowany lub dostosowywany do operacji „bezproblemowych”.
8D – Rozpoznawanie zespołowe i indywidualne:
Gdy problem zostanie całkowicie rozwiązany rozwiązany, zespół i nadzwyczajni współpracownicy muszą zostać odpowiednio wynagrodzeni i uznani. Będzie to stanowić czynnik motywacyjny dla innych pracowników.
Oto kroki metodologii 8D. Podsumowując, 8D to holistyczna, systematyczna i sprawdzona metodologia rozwiązywania problemów.