8D-problemlösningsrapport
8D är en metod för problemlösning som används globalt, främst inom tillverkningsindustrin av kvalitetsingenjörer och verksamhetschefer. Syftet med 8D-problemlösningsmetoden är att identifiera, korrigera och förhindra problem som påverkar kunder och operativ effektivitet. Det är en problemlösning som liknar PDCA-cykeln (Plan – Do – Check – Act).
8D står för 8 discipliner. Det är en metod som betonar ”Inga problem bör upprepas men fixas permanent”.
8D Problem Solving Method utvecklades ursprungligen under andra världskriget. Men det blev en officiell metod 1974, när den användes av USA Regeringen för sina militära operationer som ”Military Standard 1520”. Senare anpassades den och populariserades av Ford Motors med lätt modifiering av metoden.
Som namnet antyder har 8D åtta discipliner att alla processer eller operationer ska följa för att lösa de problem som uppstår. Resultatet av 8D är en rapport som heter ’8D-rapport’ som registrerar problemen, grundorsaken och korrigerande och förebyggande åtgärder.
Nedanstående är D: erna i 8D-tillvägagångssätt:
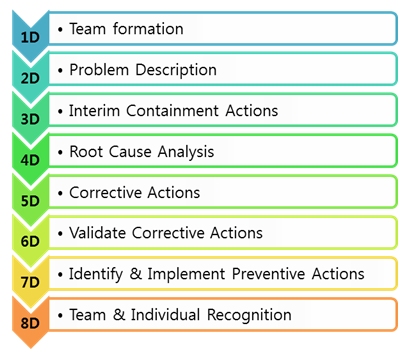
Figur 1: 8D Problemlösning Metod
1D – Team Formation:
Det första och främsta steget inte bara i 8D utan också i andra initiativ eller projekt är Team Formation, för alla initiativ kan inte lyckas utan rätt lag. Teamet som valts bör vara engagerat, kompetent, samordnat, tvärfunktionellt med representation från alla team och bör ha kunskap om 8D-metodik.
2D – Problembeskrivning:
När vi har valt laget bör vi koncentrera oss på att beskriva problemet. Teamet ska samla in detaljer om problemet för att förstå djupet av problemet. Alla detaljer ska vara data- och faktabaserade.
3D – Åtgärder för tillfällig inneslutning:
När problemet har beskrivits, innan teamet går vidare till problemlösning, bör teamet fixa effekten av problemet, särskilt på kunder. Det kan handla om att isolera de berörda föremålen, byta ut defekta delar innan det når kunderna. Detta steg är främst för att förhindra att problemet når marknaden och kunderna, vilket kan bli en konkurrensnackdel och minska kundlojaliteten.
4D – Root Cause Analysis:
Efter att ha tagit inneslutningsåtgärder bör teamet involvera i att identifiera orsaken till problemet. Metoder och verktyg som 5-Why-analys, Fishbone-diagram, Pareto-analys, 7 gamla QC-verktyg, nya QC-verktyg etc. kan användas för att identifiera grundorsaken. En viktig punkt att notera är: Oavsett vilken metod som används för RCA, ska det vara data & faktabaserat.
5D – Formulera korrigerande åtgärder:
Efter att ha kommit fram till grundorsaken bör teamet formulera korrigerande åtgärder för att åtgärda problemet. Verktyg som Brain storming, Affinity diagram etc. kan användas.
6D – Validera korrigerande åtgärder:
Efter att ha kommit till de korrigerande åtgärderna bör teamet verifiera om lösningarna är effektiva. Det finns flera verktyg som Accelerated life testing, simulation etc. tillgängliga för detta ändamål. Sedan kan lösningen implementeras i processen. Lösningsmetoden från steg 4-6 bör upprepas tills problemet elimineras helt.
7D – Förebyggande åtgärder:
Identifiera och implementera korrigerande åtgärder är bara en tillfällig lösning som håller systemet igång eller är som ”Att leva med problemet genom att vidta motåtgärder”. Den permanenta lösningen är att identifiera en potentiell långsiktig lösning som inte tillåter att problemet (liknande problem) uppstår i systemet igen. Ibland är korrigerande åtgärder en kostsam åtgärd. Förebyggande åtgärder gör förändringar i systemet, uppströms eller nedströms processer så att hela systemet modifieras eller justeras för ”Problemfria” operationer.
8D – Team och individuellt erkännande:
När problemet är helt löst måste teamet och de extra vanliga bidragsgivarna belönas och erkännas på lämpligt sätt. Detta kommer att fungera som en motivationsfaktor för andra anställda.
Detta är stegen i 8D-metoden. Sammanfattningsvis är 8D en holistisk, systematisk och beprövad metod för problemlösning.